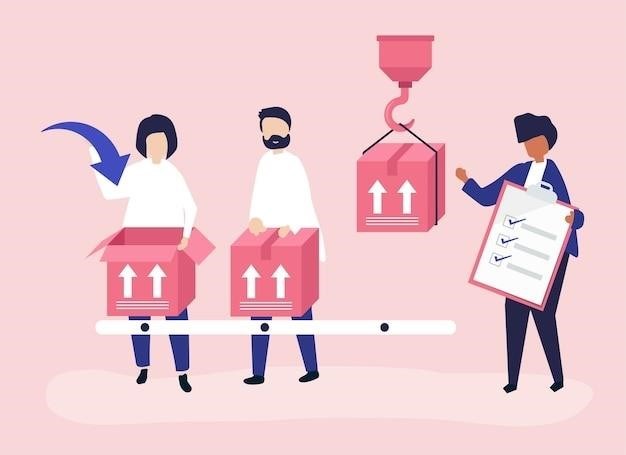
manual handling hierarchy of control
Manual Handling Hierarchy of Controlā An Overview
The hierarchy prioritizes risk elimination and reduction. It progresses from eliminating hazards entirely, through substitution and engineering controls, to administrative measures and finally, Personal Protective Equipment (PPE) as a last resort, emphasizing proactive safety.
Elimination of Hazards
The most effective approach to manual handling safety is the complete elimination of hazardous tasks. This involves a fundamental reassessment of workflows and processes. If a task inherently involves unsafe manual handling, the entire process should be redesigned to remove the need for it altogether. This might involve automation, such as using robotic systems for lifting heavy objects or conveyor belts for material transport. Alternatively, the design of products or workspaces can be modified to reduce the physical demands of manual handling. For example, rearranging workstations to minimize distances and heights involved in moving materials could significantly reduce strain and risk of injury. Ultimately, eliminating the hazard prevents the possibility of injury entirely, representing the highest level of safety.
Substitution of Tasks or Materials
If complete elimination isn’t feasible, the next priority is substituting the hazardous task or materials. This involves replacing heavy or awkwardly shaped objects with lighter, more manageable alternatives. For instance, using lighter packaging materials, implementing smaller containers, or employing wheeled carts instead of manual carrying can drastically reduce the physical strain on workers. Substituting a manual process with a mechanized one is another effective approach. This could entail using forklifts for moving pallets, overhead cranes for lifting heavy machinery, or robotic arms for repetitive lifting tasks. Even slight modifications, like replacing a cumbersome tool with a more ergonomic design, can significantly improve safety. The key is to find suitable replacements that reduce the risk of injury without compromising productivity. Careful consideration of material properties and task designs is crucial for successful substitution.
Engineering Controls for Risk Reduction
Engineering controls focus on modifying the workplace environment to minimize manual handling risks. This involves implementing physical changes to reduce the physical demands of tasks. Examples include installing conveyor belts to transport materials, using automated lifting devices like hoists or cranes for heavy loads, and designing workstations to optimize posture and reduce strain. Improving workplace layout is another key aspect. This may involve strategically placing materials to reduce travel distances, implementing ergonomic work surfaces to maintain proper posture, and ensuring sufficient space for movement to avoid obstructions and collisions. Adding mechanical aids such as powered pallet jacks or lift tables can significantly reduce the need for manual lifting. Investing in well-designed equipment is crucial; poorly designed tools or machinery can actually increase the risk of injuries. The aim is to create a safer and more efficient work environment that inherently reduces the risk of manual handling injuries, regardless of the worker’s physical capabilities.
Administrative Controls and Best Practices
Administrative controls involve implementing policies, procedures, and training programs to manage manual handling risks. These are crucial for ensuring that workers understand and follow safe handling techniques. Comprehensive training programs are essential, covering proper lifting techniques, risk assessment, and the use of available equipment. Job rotation can help to reduce strain on individual workers by distributing demanding tasks among multiple employees. Regular breaks also minimize fatigue, a significant factor in manual handling injuries. Implementing clear guidelines on load limits and appropriate handling procedures is vital, ensuring all workers are aware of safe practices. Furthermore, effective communication between management and employees is critical for identifying and addressing potential hazards. A robust system for reporting near misses and incidents helps identify areas needing improvement in workplace safety protocols. Regular monitoring of workers’ performance and feedback sessions are vital to ensure compliance with safety guidelines and to identify areas for further improvement in administrative controls. A proactive approach to administrative controls contributes significantly to a safer work environment.
Personal Protective Equipment (PPE) as a Last Resort
Personal Protective Equipment (PPE), such as gloves, back supports, and safety footwear, should only be considered after all other control measures have been implemented. PPE offers a final layer of protection but doesn’t eliminate the underlying hazard. Its effectiveness depends heavily on proper selection, fitting, and consistent use by workers. Regular inspections and maintenance of PPE are vital to ensure it remains effective and safe. Training on the correct use and limitations of PPE is essential, as it’s not a substitute for addressing the root causes of manual handling risks. Workers must understand that PPE provides only supplementary protection and doesn’t eliminate the need for safe handling techniques. Employers have a responsibility to provide appropriate PPE, ensuring it meets relevant safety standards and is suitable for the specific tasks involved. Furthermore, providing workers with information regarding the limitations of PPE and emphasizing the importance of other control measures is crucial. The reliance on PPE should always be viewed as a temporary measure while more permanent solutions are implemented to eliminate or reduce manual handling risks.
Understanding the Hierarchy’s Importance
Prioritizing hazard elimination and risk reduction is paramount for workplace safety. This systematic approach minimizes injuries, improves productivity, and fulfills legal and ethical responsibilities.
Prioritizing Prevention over Protection
The core principle underpinning the manual handling hierarchy is the strong emphasis on preventative measures. Instead of solely relying on protective equipment (PPE) as a solution, the hierarchy advocates for a proactive approach that addresses the root causes of risk. This means prioritizing the elimination of hazards whenever possible. If complete elimination isn’t feasible, the focus shifts to substituting hazardous tasks or materials with safer alternatives. Engineering controls, such as ergonomic workstation designs or the implementation of mechanical lifting aids, further reduce risk. Only after exhausting these preventative strategies should administrative controls and, finally, PPE be considered. This systematic approach ensures that the most effective and sustainable safety measures are implemented, minimizing the reliance on potentially less effective and less comfortable personal protective equipment.
By placing prevention at the forefront, organizations can significantly reduce the likelihood of workplace injuries associated with manual handling. This proactive stance not only protects workers but also demonstrates a commitment to a safe working environment, which fosters trust and improves overall morale. It’s a demonstrably more effective strategy in the long run, compared to a reactive approach that simply deals with injuries after they occur. Prevention, therefore, is not just a best practice; it’s a fundamental shift in mindset that underpins the entire manual handling hierarchy.
Legal and Ethical Obligations in Workplace Safety
Adherence to the manual handling hierarchy isn’t merely a best practice; it’s a legal and ethical imperative for employers. Legislation in many jurisdictions mandates the implementation of control measures to minimize workplace risks, including those associated with manual handling. Failure to comply with these regulations can lead to significant penalties, including hefty fines and legal action. Beyond legal obligations, there’s a strong ethical dimension to workplace safety; Employers have a moral responsibility to provide a safe and healthy working environment for their employees, ensuring their well-being is prioritized above profit maximization. Ignoring the hierarchy demonstrates a disregard for this responsibility, potentially leading to serious injuries and long-term health consequences for workers. The ethical commitment goes beyond compliance; it involves a genuine dedication to creating a culture of safety, where employees feel valued and protected.
Implementing the hierarchy not only fulfills legal and ethical duties but also fosters a positive work environment characterized by trust and mutual respect. This commitment translates to increased employee morale, reduced absenteeism, and improved productivity. Ultimately, a proactive approach to workplace safety is not only the right thing to do but also makes sound business sense.
Cost-Effectiveness of Proactive Risk Management
While implementing the manual handling hierarchy may involve upfront costs, a proactive approach is significantly more cost-effective in the long run compared to a reactive one. The financial burden of workplace accidents is substantial, encompassing medical expenses, workers’ compensation claims, lost productivity, legal fees, and potential reputational damage. A single serious injury can easily outweigh the investment in preventative measures. By prioritizing hazard elimination and risk reduction through the hierarchy, organizations minimize the likelihood of incidents, directly reducing these substantial costs. Investing in engineering controls, for example, might seem expensive initially, but it offers long-term savings by preventing repetitive strain injuries and other musculoskeletal disorders. Similarly, employee training programs, while requiring an investment of time and resources, pay dividends by creating a safety-conscious workforce that understands and adheres to proper handling techniques. The cost savings extend beyond direct financial benefits; a safer workplace improves employee morale and reduces absenteeism, leading to increased productivity and efficiency. A proactive approach, therefore, not only fulfills ethical and legal obligations but also translates into a sound financial strategy for any organization.
Practical Application of the Hierarchy
Real-world application requires a thorough risk assessment, identifying hazards and selecting appropriate control measures from the hierarchy, prioritizing prevention, and regularly reviewing effectiveness.
Case Studies and Real-World Examples
Consider a warehouse where workers repeatedly lift heavy boxes. Eliminating the hazard might involve automating the process with conveyors or robotic arms. If complete elimination isn’t feasible, substituting lighter boxes or using smaller, more manageable containers could significantly reduce the risk. Engineering controls could involve installing ergonomic workstations or using lifting aids like pallet jacks. Administrative controls could include implementing proper lifting techniques training, rotating tasks to prevent repetitive strain injuries, and scheduling adequate rest breaks. Finally, as a last resort, PPE such as back supports might be provided. Another example is a nursing home where staff frequently transfer patients. Elimination isn’t possible, but substitution could involve using patient hoists. Engineering controls could be improved flooring for better traction, and administrative controls could be providing additional staff for patient transfers and implementing safe patient handling protocols. PPE, such as gloves and lifting belts, would be a final measure. These examples showcase how the hierarchy prioritizes preventative measures. Careful consideration of each level ensures a safer working environment, minimizing the reliance on PPE as the primary safety measure.